How are carpet tiles made?
Here you can find out how a carpet tile is made!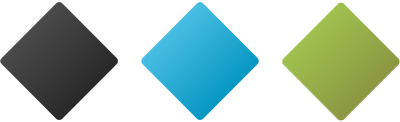
This is how carpet tiles are made
The production process for carpet tiles is complex and includes more steps than the production of classic carpet by the meter. An excellent coordination of the raw materials and the production steps on each individual product type is necessary in order to achieve a high quality of the carpet tile produced in the end.
The choice of upper material determines the production process
The final design of the carpet tiles is already determined with the first production step: The choice of the upper material in the form of textile roll goods (velor, loop, hair tile, …) determines which material composition and quantities are required to build up and stabilize the back equipment. Finally, the machinery and the other production steps are adapted to this.
The textile upper material used as the base material is identical to that of a classic carpet on the roll and is usually a little over 2 m wide, so that through the end appropriate cuts can always be made for carpet tiles in formats of 50 x 50 cm, 100 x 100 cm or 100 x 200 cm.
„ Not every carpet tile is produced in the same way: The upper material determines which requirements the backing must meet. ” Sebastian Blomberg Product Manager
The “wedding”: fusion of upper material and back
Because of their high dead weight and good dimensional stability, high-quality carpet tiles have “self-laying” properties (more on the subject on the “Installation” page), and they are also robust against cold and exposure to heat.
In order to achieve these quality features, a multi-layered backing is required: First, the raw material is “bathed” with the underside in liquid bitumen using a roller system. A first fine bitumen layer is evenly applied to the material, which creates the first firmness of the later carpet tile after the bitumen has dried out.
Stability through melted fiberglass fabric
In the next step, a fiberglass cover is placed loosely on the bitumen layer, which, supplemented by a second bitumen application in a second bath, completes the technically necessary structure of the back construction. As part of the final production process, a cover fleece is laminated on for finishing 2 to 3 seconds after the liquid bitumen has been applied, on which batch numbers and arrows are printed to indicate the laying direction.
The back consists of two layers of bitumen with a fiberglass cover fused in between and a fleece cover. The exact amounts of material must be individually adapted to each collection and the tile format to be produced. This is the only way that carpet tiles end up with their unique properties, which distinguish them from traditional carpeting by the roll.
Cutting and formatting – finishing
In the further course of production, the cutting of the “roll goods” into the desired formats – usually 50 x 50 cm. The material runs through a section in which the rapidly rotating knife cuts the web material from below into the desired sizes. The dimensional accuracy is precisely controlled by laser technology. The then finished “textile modules” are only packed into the boxes and labelled with the help of robots.
If you have any questions, just give us a call or send us an email. Our competent service team is available to help you.